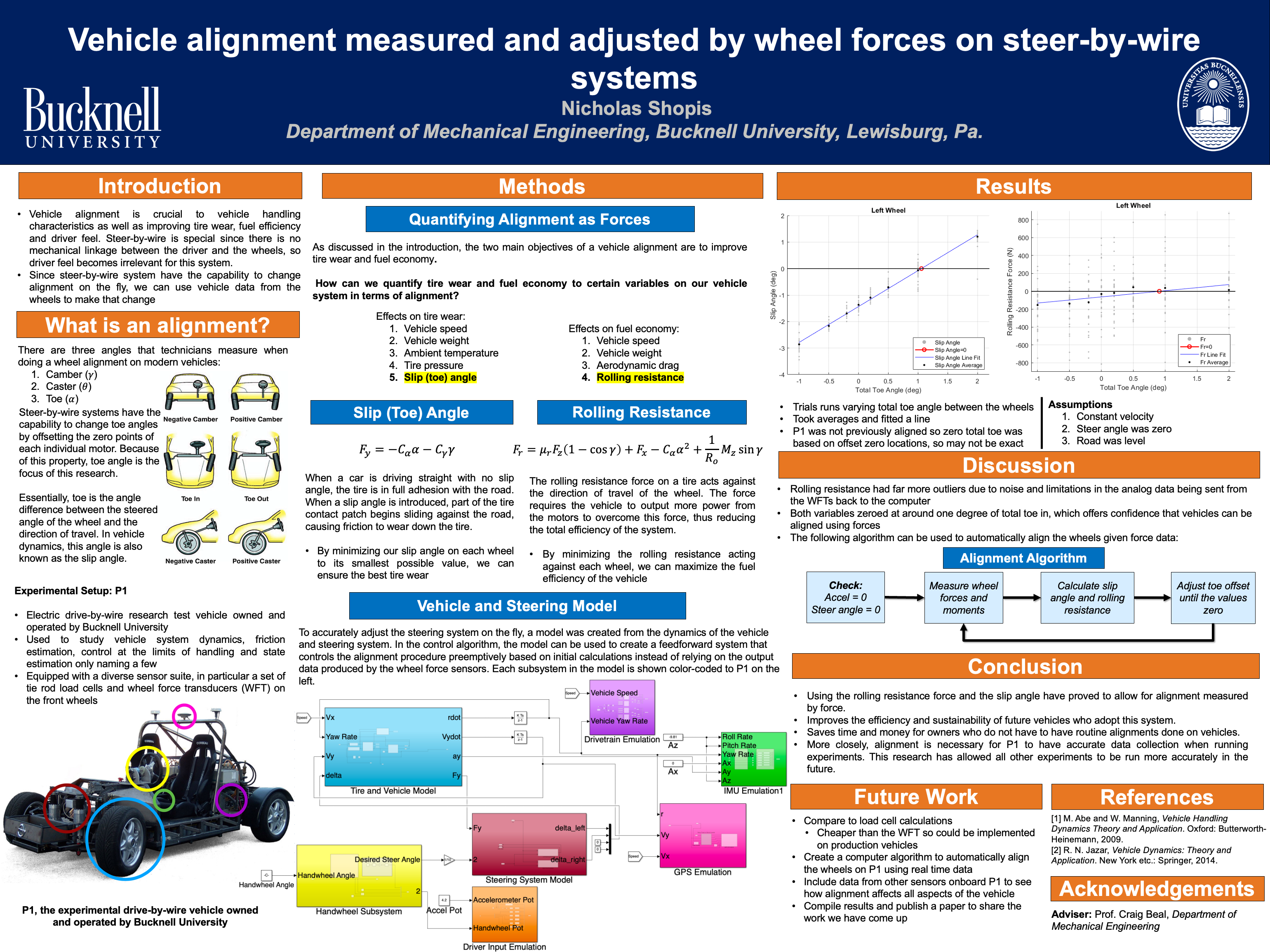
Vehicle alignment measured and adjusted by wheel forces on steer-by-wire systems
Author:
Nick Shopis ’25Co-Authors:
Faculty Mentor(s):
Craig Beal, Mechanical EngineeringFunding Source:
Kalman FundAbstract
To optimize fuel efficiency and tire wear, all modern automotive vehicles have service intervals after which the front wheels are re-aligned. An offset alignment causes unwanted forces and moments on the wheels and steering system that reduce fuel efficiency and increase tire wear. An alignment procedure is normally done using a machine that can measure the angle of wheels, which are adjusted using mechanical linkages on the vehicle. New electronic steering systems, such as steer-by-wire, offer a new alternative to this angular alignment procedure. Since these steering systems can control the angle of wheels independent from the steering wheel position, the alignment of the wheels can be done without adjusting mechanical links. By measuring forces on the wheels with onboard sensors, a relationship can be developed between them and the correct alignment angle of the wheel. A vehicle model was created and tested against an electric research vehicle equipped with a steer-by-wire system. The research vehicle was equipped with a set of wheel force transducers that were able to measure the forces and moments on the front wheels in all directions. It was found that adjusting the wheel angle to minimize both the rolling resistance and slip angle produced the highest increase in fuel efficiency and the largest decrease in tire wear. Additionally, this vehicle model serves as a bench block for an active alignment algorithm that can take real-time wheel force measurements and automatically adjust the steering systems based on these loads.